The Complete Guide to Building an Operational Excellence Framework: Best Practices
Master the essentials of operational excellence framework implementation with proven strategies from industry leaders. Learn how to build, deploy, and measure success in your organization. meta t: The Complete Guide to Building an Operational Excellence Framework: Best Practices and Implementation published: No slug: operational-excellence-framework
Understanding the Evolution of Operational Excellence
The concept of operational excellence has become essential for business success across many different industries. Rather than a fixed endpoint, achieving excellence requires ongoing refinement and adaptation. Starting from its beginnings in Japanese manufacturing and evolving into today's comprehensive framework, this history helps us understand how businesses can apply these principles effectively.
From Manufacturing Roots to Modern Business Systems
The story begins in post-World War II Japan, where companies like Toyota developed new production methods focused on quality and efficiency. Their systems introduced lean manufacturing and Kaizen (continuous improvement), which set new global standards for production excellence. These approaches emphasized reducing waste, improving processes, and giving employees more ownership - creating an environment where improvement happens naturally.
Toyota's work to eliminate defects through its Toyota Production System showed remarkable results in quality and efficiency, inspiring manufacturers worldwide. In the 1970s, Dr. Joseph M. Juran introduced formal Operational Excellence (OE) concepts while teaching Japanese business leaders about quality improvement. These ideas gained significant attention in the United States during the 1980s as companies faced increasing competition. Learn more about this history in the Operational Excellence Wikipedia article.
Adapting to Modern Challenges
The meaning of operational excellence has grown significantly over time. What started as manufacturing-focused practices now covers many business areas including service delivery, customer experience, and innovation. This broader scope reflects an understanding that excellence means creating value across the entire organization, not just improving efficiency. As a result, new frameworks have emerged to address modern business complexities.
Modern operational excellence now includes digital tools, data analysis, and flexible working methods. These updated approaches recognize how important technology, data-based decisions, and adaptability are for maintaining high performance.
The Core Principles of a Modern Framework
While operational excellence continues to evolve, several key principles remain constant. These fundamentals provide the base for building an effective operational excellence framework:
Customer Focus: Making customer needs and expectations the top priority
Process Optimization: Finding and removing inefficiencies in all processes
Data-Driven Decision-Making: Using concrete information to guide choices and measure results
Employee Empowerment: Giving staff the tools and authority to drive improvements
Cultural Transformation: Building an environment that values excellence and learning
These principles work together to create ongoing improvement. A successful operational excellence framework needs to connect these ideas across the whole organization. This creates a system where getting better becomes part of the company culture, leading to lasting growth and success.
Essential Tools and Methodologies That Drive Excellence
Building an effective operational excellence framework requires carefully selecting and combining the right tools and methods. Success comes from understanding how different approaches complement each other and choosing ones that align with your organization's specific goals.
Key Methodologies for Operational Excellence
Let's explore some proven methods that help organizations achieve operational excellence through systematic improvement.
Lean Management: This approach focuses on removing waste while maximizing value for customers. By identifying and eliminating activities that don't add value, organizations can improve efficiency and reduce costs.
Six Sigma: This method uses data and statistics to minimize defects and variations in processes. Created at Motorola in the 1980s, Six Sigma aims for just 3.4 defects per million opportunities. General Electric later combined it with their Change Acceleration Process (CAP) and DMAIC methodology to boost process quality. Learn more about this approach in Six Sigma and Operational Excellence.
Kaizen: This system promotes ongoing improvement through small, steady changes. It creates a workplace culture where every employee helps spot and implement better ways of working.
Theory of Constraints (TOC): This method focuses on finding and fixing bottlenecks that limit performance. By systematically addressing constraints, companies can improve their output and efficiency.
Integrating Tools and Methodologies
While these methods provide valuable frameworks, practical tools help turn theory into action.
Value Stream Mapping: This visual tool shows each step in delivering products or services. It helps teams spot bottlenecks, repeated work, and areas needing improvement.
Root Cause Analysis: Methods like the "5 Whys" help teams find the real source of problems. This allows for lasting solutions rather than quick fixes.
Process Automation: Using technology for repetitive tasks reduces errors and frees up staff time for more valuable work.
Adapting the Framework
There's no single perfect approach to operational excellence. Your framework should match your organization's size, industry, and current capabilities. Small companies might start with basic Lean principles, while larger ones may need multiple methods working together.
Building a culture of improvement is key to success. This means getting employees involved, providing good training, and measuring progress clearly. With ongoing commitment, your operational excellence framework will keep delivering value as your organization grows and changes.
Creating a Culture That Embraces Excellence
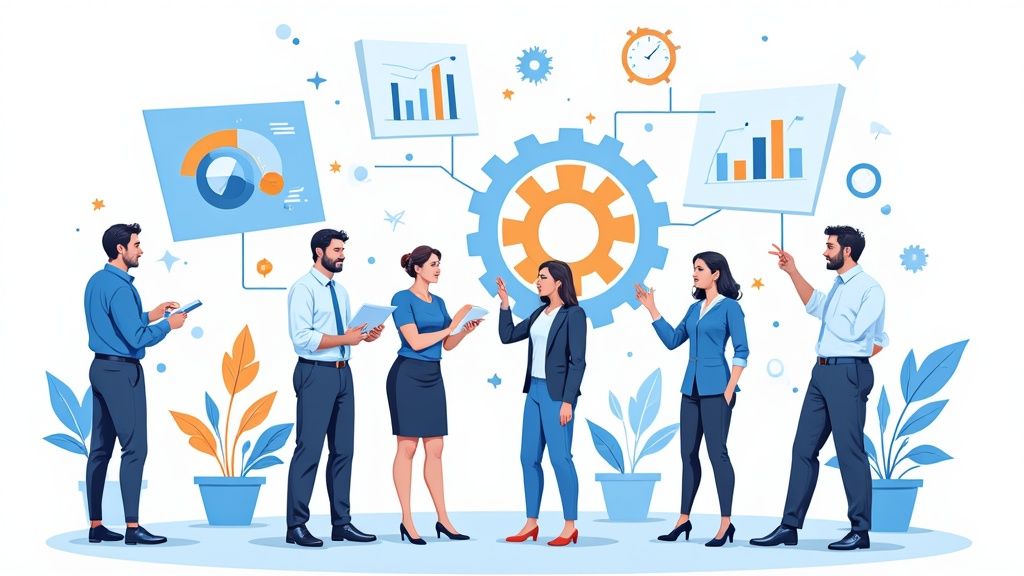
Moving to an operational excellence framework takes more than new processes - it requires shifting how people think and work. Creating lasting change means building an environment where improvement becomes a natural part of daily work. Let's explore practical ways to build this type of culture.
Building Buy-In From the Ground Up
Getting everyone involved makes all the difference. The people doing the work each day often have the best ideas for making things better. Smart organizations actively ask for their input, clearly explain how the changes will help, and recognize good ideas. This helps employees feel ownership over improvements rather than having changes forced on them.
Leaders play a crucial role too. When executives visibly support and participate in improvement work, it shows the whole organization this matters. They need to provide resources, remove obstacles, and consistently communicate why excellence matters. This combination of bottom-up engagement and top-down support creates momentum for positive change.
Recent research shows more companies are focusing on operational excellence. 57.9% of organizations reported increased adoption of these methods. The push comes from rising customer expectations and competitive pressures. Notably, 44.3% of companies use these approaches specifically to improve customer experience by removing friction points. For more details, check out The Global State of Operational Excellence.
Developing Sustainable Improvement Habits
Making improvement part of daily work beats one-off projects. This means having clear ways to spot, prioritize and implement better ways of working. Regular team meetings focused on solving problems, combined with proven methods like Kaizen or Lean, help make improvement routine. Just like building any good habit, it takes consistent practice over time.
Measuring Cultural Evolution
Tracking progress and showing real results keeps people motivated. Pick metrics that connect to business goals and share updates openly. When people see positive changes happening, it reinforces good habits. Regular feedback through surveys and discussions also helps spot where more support is needed.
Fostering an Environment of Learning
Strong cultures welcome new ideas and see setbacks as chances to learn. Create space for trying new approaches, celebrate learning from failures, and encourage smart risk-taking. Offer training resources, connect newer employees with experienced mentors, and recognize both successes and productive failures. This builds an organization that keeps growing and adapting as needs change.
Implementing Excellence Across Different Industries
Applying operational excellence principles requires careful customization for specific industries. Different sectors face unique requirements, regulations, and constraints that shape how these frameworks must be adapted. Let's explore how successful companies apply these concepts across major sectors.
Manufacturing: Precision and Efficiency at Scale
Manufacturing companies focus heavily on lean manufacturing principles to drive operational excellence. The emphasis is on removing unnecessary steps, minimizing inventory waste, and optimizing workflow. Many adopt just-in-time inventory systems to better match production with demand while reducing storage expenses. Smart automation helps standardize processes and maintain consistent quality standards.
Healthcare: Quality and Patient-Centric Care
Healthcare organizations must balance exceptional patient care with strict regulatory requirements. Their operational excellence programs prioritize patient safety and consistent treatment protocols. Simple tools like pre-surgery checklists have shown remarkable results in reducing complications. Modern healthcare facilities also use advanced analytics to monitor patient outcomes and spot opportunities for improvement.
Technology: Innovation and Agile Development
Tech companies need operational frameworks that support rapid development and frequent updates. Many adopt Agile and Scrum methodologies to break large projects into manageable pieces. This approach enables quick iteration based on user feedback while maintaining high quality standards. Teams can respond swiftly to market changes without sacrificing reliability.
Service Industries: Customer Experience and Personalized Service
Service businesses succeed by delivering outstanding customer experiences. Their operational excellence efforts focus on creating smooth, personalized interactions at every touchpoint. Many implement CRM systems to track preferences and engagement history. Data analytics help identify friction points and opportunities to exceed customer expectations.
Adapting Frameworks to Unique Environments
The pharmaceutical industry offers an interesting case study in framework adaptation. Historical regulatory constraints and cost structures initially limited adoption of approaches like Six Sigma and Lean. As cost pressures grew, companies began implementing targeted improvements through Total Productive Maintenance (TPM) and Technical Performance Measurement. Today, pharmaceutical manufacturers integrate Total Quality Management (TQM) principles across their operations to ensure stable, compliant processes. Learn more about operational excellence in pharmaceuticals
Success requires carefully matching operational excellence approaches to each industry's specific needs and constraints. By thoughtfully adapting proven frameworks, organizations can improve efficiency while achieving better outcomes - whether that's higher quality products, safer patient care, or more satisfied customers.
Measuring and Sustaining Your Excellence Journey
Success in operational excellence requires consistent measurement and improvement. Organizations need to track progress, adapt processes, and build supportive cultures. This section explores practical ways to monitor results and create lasting positive change.
Developing Meaningful KPIs
Key Performance Indicators (KPIs) help track progress toward your goals. Choose metrics that directly connect to what matters most. For customer-focused goals, measure retention rates or Net Promoter Score (NPS). For operations, track cycle times or defect rates. Good KPIs share three key traits: they're relevant to goals, easy to measure, and tied to strategy.
Implementing Effective Measurement Systems
With KPIs defined, you need reliable ways to gather and analyze data. This involves setting up measurement tools, creating standard data collection methods, and training teams on proper data handling. Quality data leads to quality decisions. Your measurement system should provide clear insights that let you spot issues early and make smart adjustments.
Maintaining Momentum in Your Excellence Journey
Success takes more than just watching numbers - it requires building a culture where everyone helps improve things. Regular check-ins, open feedback channels, and celebrating wins all help keep energy high. Try running focused improvement sessions like Kaizen events to solve specific problems quickly. When you notice and reward good ideas, people stay motivated to find better ways of working.
Building Sustainability Through Systematic Review
Like maintaining any valuable asset, excellence programs need regular care and updates. Set up routine reviews to check how well things work and what needs changing. This might mean regular audits, asking stakeholders for input, and studying what works well in similar organizations. Think of it like home maintenance - regular upkeep prevents bigger problems later.
Governance Structures and Continuous Learning
Clear roles and decision-making processes help maintain progress over time. Set up clear guidelines for who handles what in your excellence program. Equally important is creating an environment where learning thrives. Encourage teams to share knowledge, provide training opportunities, and stay current with industry changes. Building these good habits helps organizations adapt and grow stronger over time.
Improving Operations Through Modern Technology
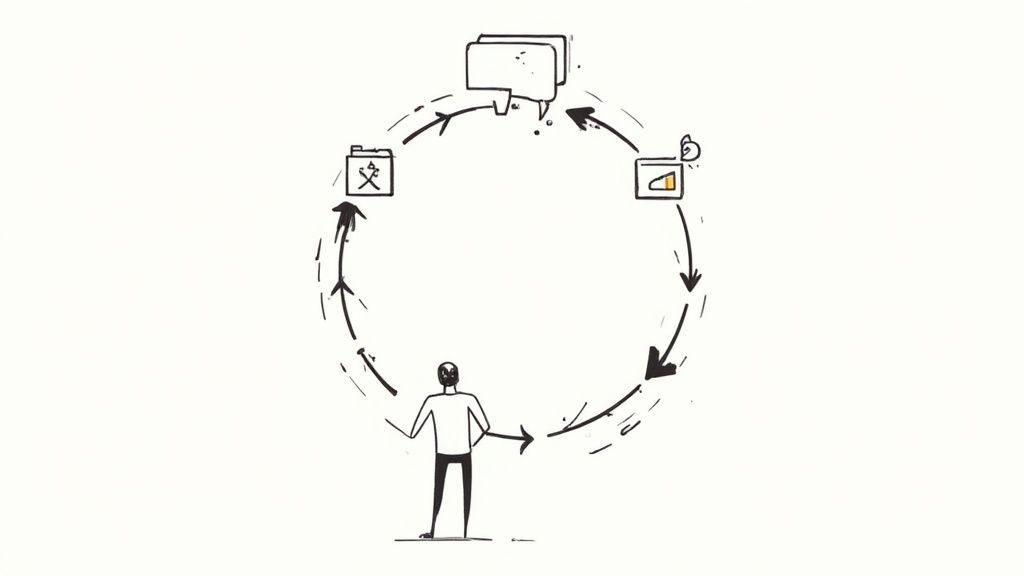
New tools and systems are changing how businesses work and improve their operations. Companies need to update their methods while keeping their core focus on quality and efficiency. This means carefully choosing the right technologies that align with business goals.
Smart Technology for Better Results
Modern tools open up new ways to improve business processes. Artificial Intelligence (AI) helps spot patterns in large amounts of data and catch problems early. Machine learning takes over routine tasks, which lets employees focus on more important work that needs human skills.
Advanced data tools help teams track how well things are working in real-time. Instead of guessing what needs fixing, managers can look at actual numbers and facts. This makes it much easier to solve problems and keep making things better over time.
Making New Technology Work for You
Adding new tools takes careful planning. Start by looking at what your business really needs and which problems need solving first. Break big changes into smaller steps to help everyone adjust. Focus on fixing one issue at a time rather than changing everything at once.
For example, if keeping track of inventory is difficult, try starting with a simple online tracking system. This focused approach lets you see how well new tools work before making bigger changes.
Picking the Right Tools
When choosing new technology, think about:
How much it costs
How hard it is to set up
What training people will need
How it fits with current systems
Try new tools on a small scale first. Run a test with a small team or department before rolling out changes to everyone. This helps avoid problems and shows if the technology actually helps.
Real Success Stories
Many businesses have improved by using new technology wisely. Some factories create digital copies of their production lines to test changes safely. This helps them fix issues without stopping real work.
Hospitals now use smart tools to help doctors make better decisions. These systems look at patient information and medical images to assist with diagnosis. These examples show how new technology can make real improvements across different types of businesses.
Looking to improve your work methods? Obsibrain helps Obsidian users manage tasks, take notes, and track goals more effectively. Learn more at Obsibrain.
Last updated
Was this helpful?