10 Proven Business Process Improvement Methods That Drive Success
Master proven business process improvement methods that transform organizations and deliver measurable results. Discover field-tested insights from industry experts on implementing, measuring, and scaling process improvements. meta t: 10 Proven Business Process Improvement Methods That Drive Success published: No slug: proven-business-process-improvement-methods-drive-success
Understanding The Evolution of Business Process Improvement
The field of business process improvement (BPI) has come a long way since its early days. What started as simple efforts to make individual tasks more efficient has grown into something much broader. Organizations now look at how all their processes work together to achieve key business goals, rather than just fixing isolated issues. This shift reflects a deeper understanding that connected processes have far greater impact on overall business success.
From Isolated Gains to System-Wide Optimization
Early BPI efforts often missed the bigger picture. Teams would focus on improving one department or process without considering how changes affected other areas. For example, speeding up production in one area sometimes created bottlenecks downstream. Modern business process improvement methods take a more complete view, emphasizing collaboration across departments and examining how processes connect. This helps companies make lasting improvements that benefit the entire organization.
The Rise of Data-Driven Decision-Making
Data has become essential to how companies improve their processes. While past decisions often relied on gut feelings or limited observations, today's organizations can use advanced analytics to guide their choices. Teams can now track key performance indicators in real-time, quickly spot problem areas, and measure exactly how well their changes work. The growing importance of smart process management shows in the numbers - 74% of businesses report increased interest in business process management (BPM), mainly to boost efficiency and reduce costs. Experts expect the global BPM market to reach $14.4 billion by 2025, growing 10.5% annually. Learn more about BPM trends and statistics.
The Human Element of Transformation
Despite all the advances in methods and data analysis, people remain at the heart of successful process improvement. Creating lasting change requires engaging employees at every level, maintaining open communication, and giving teams the power to suggest and implement improvements. This means business process improvement methods must consider both technical needs and human factors. Companies need solid change management, proper training, and ongoing support to get everyone on board. True transformation happens when both processes and people's mindsets evolve together.
Core Methodologies That Drive Process Excellence
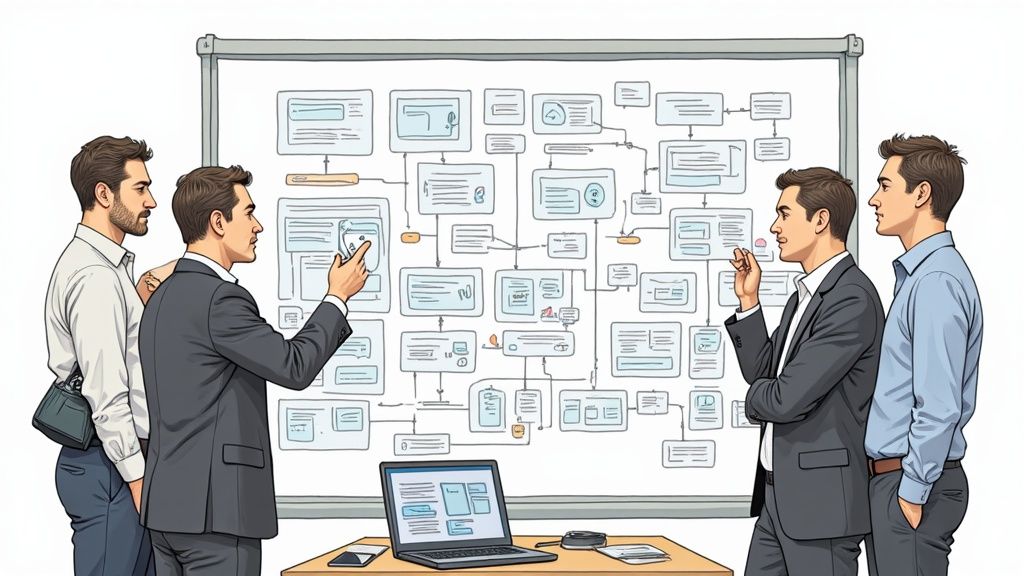
Smart businesses know that specific methods help them run better. Let's explore the proven approaches that companies use to improve how they work. These methods give clear steps for finding problems, analyzing them, and making real improvements.
Lean Methodology: Eliminating Waste for Maximum Value
Lean methodology started at Toyota and focuses on removing anything that doesn't add value. This includes more than just physical waste - it targets wasted time and effort too. For example, companies often find they can remove unnecessary paperwork, cut down approval steps, or fix duplicate data entry. By focusing on what truly matters to customers, companies become faster and more responsive to what people need.
Six Sigma: A Data-Driven Approach to Process Perfection
Six Sigma stands out as a precise way to improve business processes. This method uses data to spot and fix problems, aiming for near-perfect results - just 3.4 defects per million opportunities. Companies that use Six Sigma follow clear steps: measure current performance, analyze what's wrong, make improvements, and keep checking that things stay fixed. You can learn more about different improvement methods at KainExus's process improvement guide.
Total Quality Management (TQM): Embedding Quality in Every Process
Total Quality Management looks at the big picture of quality improvement. Instead of just fixing problems when they pop up, TQM creates an environment where everyone owns quality - from top managers to front-line workers. This means building quality checks into every step, not just at the end. When companies use TQM well, employees actively spot ways to make things better and help create better products and services.
Hybrid Approaches: Combining the Best of Different Worlds
Most companies find that using just one method isn't enough. That's why many mix and match different approaches to solve their specific problems. For instance, a company might use Lean to cut down on waste while also applying Six Sigma tools to reduce mistakes. The key is picking the right mix of methods that work for your specific situation and needs. Success comes from knowing which tools to use and how to use them well to create lasting improvements.
Industry-Specific Implementation Strategies
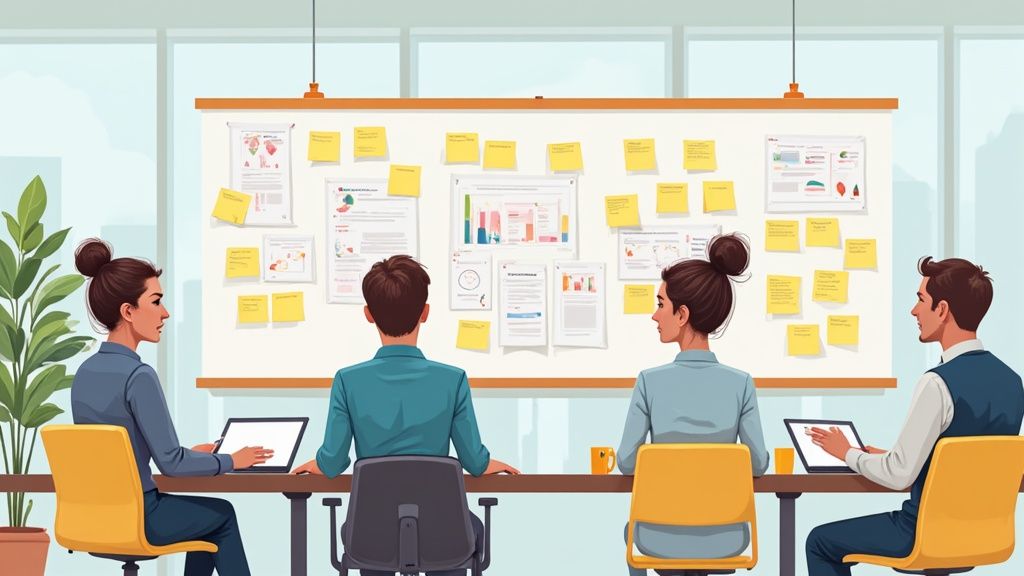
While business process improvement methods share common foundations, each industry needs a customized approach based on its specific requirements and constraints. Understanding these differences helps organizations apply these methods effectively and achieve better results.
Healthcare: Balancing Quality with Patient Care
Healthcare organizations must put patient safety first when improving processes. For example, while scheduling systems can boost efficiency, they need flexibility to handle emergencies and individual care needs. Privacy regulations and data security also shape how changes get implemented.
Key considerations include:
Maintaining quality of care during process changes
Meeting strict regulatory requirements
Protecting sensitive patient data
Ensuring staff can focus on patients
Manufacturing: Integrating Improvement with Automation
Manufacturing companies often combine process improvements with automated systems to boost results. For example, using Lean principles alongside robotic systems can reduce waste while increasing production quality. Success requires careful planning to:
Train workers on new technologies
Minimize production disruptions
Test changes before full rollout
Monitor and adjust implementations
Service Industries: Focusing on Customer Experience
Service businesses aim to make customer interactions smoother and more satisfying. Online booking systems and self-service options can reduce wait times and friction points. Data analysis helps understand customer needs and preferences to deliver better service.
Common improvements include:
Simplified booking and payment processes
Reduced wait times
More personalized service
Better communication channels
BFSI: Driving Efficiency and Reducing Errors
Banks, financial services, and insurance companies lead in adopting Business Process Management (BPM). 35% of BFSI companies use BPM to improve their operations - the highest rate across industries. Learn more about BPM adoption rates.
The results speak for themselves:
40% of organizations report fewer errors
More accurate decision-making
Better regulatory compliance
Faster transaction processing
Adapting Methodologies to Your Specific Context
No matter your industry, success requires fitting standard methods to your organization's unique needs. This means:
Understanding your specific challenges
Adjusting approaches to match your goals
Creating clear implementation plans
Measuring results and making improvements
Regular monitoring and updates help ensure lasting positive changes that benefit both operations and outcomes.
Using Technology To Make Processes Better
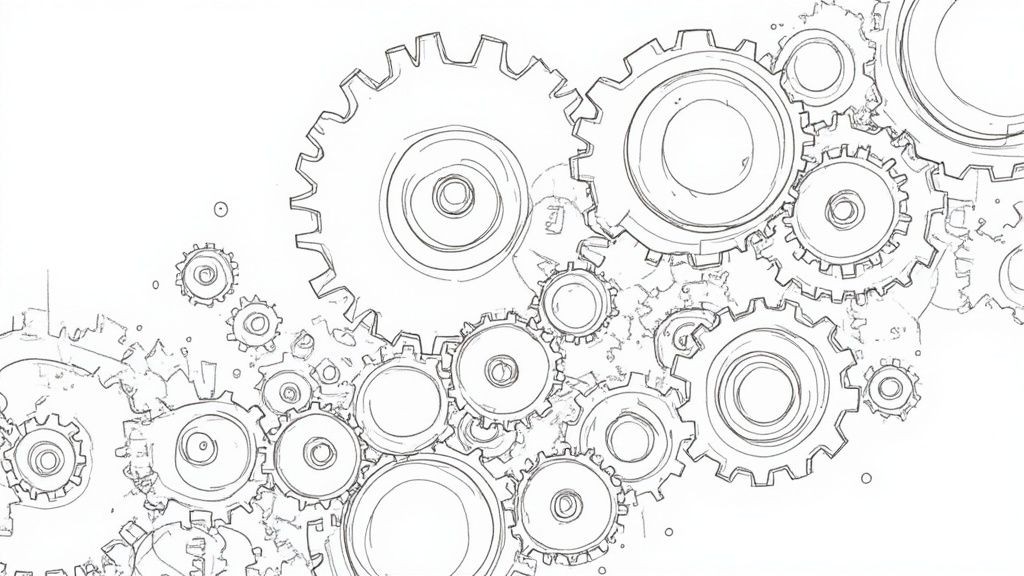
When it comes to improving business processes, technology has become essential. But it's not just about replacing manual work with computers - it's about making processes smarter and more responsive. Let's look at how companies are using different technologies to boost their process improvement efforts.
Making Tasks Easier With RPA
Robotic Process Automation (RPA) works like a digital assistant that handles repetitive jobs. For example, it can take care of data entry, process invoices, or respond to basic customer questions. This gives employees more time to work on complex tasks that need human judgment. But RPA is just one piece of the puzzle - Artificial Intelligence (AI) and Machine Learning (ML) are opening up even more possibilities.
Smart Automation Through AI and ML
AI can spot patterns in large amounts of data that humans might not notice. Take a retail company using AI to predict which customers might stop shopping with them, or a manufacturer using it to make their supply chain run better. ML takes this further by learning from new information over time - like a customer service system that gets better at answering questions the more it's used.
Finding The Right Tech Tools
Different organizations need different technology solutions. A neighborhood bakery might just need basic automation for order tracking, while a global company could benefit from advanced AI systems for market analysis. The key is to look carefully at your current processes, spot the bottlenecks, and pick tools that match your business goals.
Making New Technology Work Well
Adding new technology takes more than just installing software. It needs to work smoothly with your existing systems and your team needs to know how to use it. Clear communication and proper training are crucial. For example, when a company adds RPA for processing orders, they need to make sure the system connects properly with their inventory database and train staff to handle any unusual cases the automation can't process.
Checking If Technology Is Helping
It's important to track whether new technology is actually making things better. Keep an eye on key numbers like time saved, money saved, and whether customers are happier. This helps you fine-tune your processes and make sure you're getting good value from your tech investments. By combining solid business process improvement methods with the right technology, companies can make lasting positive changes to how they work.
Building Sustainable Process Excellence
Creating lasting improvements isn't about quick fixes - it's about weaving continuous improvement into your company's DNA. Success comes from shifting focus from reactive problem-solving to proactively seeking better ways of working every day.
Establishing a Governance Structure
Every successful improvement program needs clear guidelines and roles. Setting up a governance framework helps teams understand who makes decisions, how to prioritize initiatives, and how progress gets tracked. Think of this as your playbook for making positive changes stick across the organization.
Fostering a Culture of Continuous Improvement
One-off process tweaks rarely deliver sustained results. Real change happens when improvement becomes second nature to everyone. This means creating spaces where people can share ideas freely - like regular team feedback sessions, suggestion boards, and programs that recognize great improvement ideas. When staff see their input making a difference, they become active partners in making things better.
Maintaining Momentum and Handling Resistance
Even great initiatives can lose steam over time. Keep energy high by celebrating wins both big and small, sharing progress updates that highlight real impact, and regularly reinforcing the "why" behind changes. When you encounter pushback - which is normal - address concerns openly. Good training and clear examples of how changes help individual employees can turn skeptics into supporters.
Measuring and Tracking Progress
Without solid metrics, it's impossible to know if changes are working. Set up clear key performance indicators (KPIs) that connect directly to your business goals. Regular tracking helps spot what's working well and what needs adjustment. This fact-based approach proves the value of your improvement work and keeps efforts focused on what matters most.
Scaling Improvements Across the Organization
Taking successful changes from one team to the entire company takes careful planning. Start small with pilot projects, gather feedback, refine your approach, then expand step by step. Clear communication and documented best practices help maintain quality as you roll out changes. This measured approach prevents overwhelming people and builds lasting positive change that sticks.
Emerging Trends Shaping Process Excellence
Process excellence today requires looking beyond current methods to understand what's coming next. Let's explore the key trends changing how organizations improve their processes and prepare for future challenges.
The Rise of Hyperautomation
Hyperautomation represents the next evolution in process automation by combining Robotic Process Automation (RPA), Artificial Intelligence (AI), and Machine Learning (ML). Think of it like having a smart system that not only handles routine tasks but gets better at optimizing processes over time by learning from data. Organizations can now automate even their most complex workflows, leading to major gains in efficiency.
Process Mining: Uncovering Hidden Insights
Process mining helps organizations see how their processes actually work in practice, not just in theory. By analyzing system logs and data, teams can map out detailed process flows and spot problems they might otherwise miss. For example, process mining might reveal that an extra approval step is causing significant delays in order processing - something that traditional process mapping could overlook.
The Democratization of Process Improvement
Process improvement is no longer just for specialists and consultants. The democratization of process improvement puts tools and methods in the hands of frontline employees who know the work best. By giving teams easy-to-use tools and encouraging everyone to suggest improvements, organizations tap into their employees' practical knowledge and experience.
The Focus on Customer Journey Mapping
Understanding the customer's experience has become central to process improvement. Customer journey mapping tracks each interaction a customer has with your organization, from first contact through post-purchase support. This helps identify exactly where processes need to change to better serve customers. A good example is when mapping reveals that customers consistently abandon their shopping carts at the same point - a clear signal that this process needs fixing.
Agile Process Improvement
Taking cues from software development, agile process improvement breaks big changes into smaller, manageable pieces. Instead of long, complex projects, teams make incremental improvements and gather feedback quickly. This approach helps organizations stay flexible and responsive as business needs change.
Integrating Emerging Trends With Existing Methodologies
These new trends work best when combined with proven business process improvement methods like Lean, Six Sigma, and TQM. Smart organizations blend new techniques with tested approaches to create more effective improvement programs. This balanced approach helps teams get the best results from both new and established methods.
Ready to optimize your workflows and achieve lasting process improvements? Obsibrain offers a centralized platform to streamline your task management, goal setting, and daily planning. Learn how Obsibrain can help you achieve peak productivity by visiting https://www.obsibrain.com
Last updated
Was this helpful?